Cement
Lime is a powder made of calcium oxide (CaO) produced by
baking the carbonate out of calcite in limestone.
Silica is a generic term for
SiO2 - quartz.
Alumina is aluminum oxide Al2O3, common in
clay and many silicate minerals.
Calcine
means to heat a rock up to a very high temperature - hot enough to burn off
any water and carbon, but not hot enough to actually melt the rock. We produce lime by calcining
limestone.
(Limestone / Calcium
Carbonate) CaCO3 + heat ®
(Lime/Calcium
Oxide) CaO + CO2(g)
Calcite
Lime
Portland Cement is the most common type of cement used today due to its
vastly greater strength compared to other cements. The ingredients are essentially the same
as Natural Cement (lime, silica, alumina, and iron
oxides), but the calcining process is
done at a much higher temperature. The precise proportion of ingredients is
important. In most cases, this
requires mixing of several rocks together, although the limestone in select
regions naturally contains the appropriate elements in the appropriate
proportions.
The
powdered product is primarily a mixture of tricalcium silicate (3CaO ·
SiO2), tricalcium aluminate (3CaO · Al2O3), and
dicalcium silicate (2CaO · SiO2), in varying proportions, along with
lesser amounts of magnesium and iron compounds and gypsum. Gypsum is often
added to slow the hardening process.
Dolomite (CaMg(CO3)2) and alkalis are harmful
impurities.
The compounds in active cement are
unstable together. When water is
added, they rearrange their structure and interact chemically to form
interlocking crystals of calcium-aluminum-silicates that bind together the
particles of sand or stone.
The Kiln, a giant cylindrical pipe
about 15 feet or so in diameter that slowly turns. The kiln is on a gentle incline, so that
raw materials dropped in one side slowly mix and make their way down to the
lower end. Pulverized coal is blown
up into the kiln from the lower end as fuel to heat the mixture and calcine the
limestone. Monitoring the temperature of the mix, composition of exiting gasses,
etc. constantly is essential. Using a petrographic microscope, too,
which is used to analyze the shapes and proportions of the crystals of
tricalcium silicate, tricalcium aluminate, and
dicalcium silicate when the cement is cured is also a strong factor in
determining the strength of the cement.
The the
ball mills are where the clinker is grinded into a powder. Ball mills are big, spinning cylinders
that contain cannon balls made of hard steel. When they put clinker in the cylinders,
the spinning tube causes the balls to bounce around and break up the clinker
into a powder. The powder is mixed
with gypsum (which slows the hardening process and allows for better control
during pouring at the construction site)
When producing cement, the chemical composition of cement is
controlled by the content of silica (SiO2), lime (CaO), alumina
(Al2O3) and iron (Fe2O3).
These oxides become characteristic clinker minerals which during the
addition of gypsum will be ground to cement. Portland cement is made up of
four main clinker compounds: Tricalcium silicate
(allite) (C3S), Dicalcium silicate
(belite)(C2S), Tricalcium aluminate
(C3A) and Tetra-calcium aluminoferrite
(C4AF). Where C stands for calcium oxide, S for silica, A for
alumina, and F for iron oxide. Small amounts of uncombined lime, magnesia,
alkalis and minor amounts of other elements (titanium, manganese etc.) are
also present. The composition of Portland cements falls within the range
of 60 to 67 percent lime, 17 to 25 percent silica, 2 to 8 percent alumina,
and 0 to 6 percent iron oxide together with 1 to 7 percent sulphur
trioxide, derived mainly from the added gypsum, 0.1 to 5 percent magnesia,
and 0.1 to 1.5 percent alkalis. The chemical composition of
cement influences the characteristics of cement. The clinker mineral
C3S is the head clinker component in cement. The strength
developed by Portland cement depends on its composition of C3S,
C2S, C3A, C4AF and the fineness (Blaine)
to which it is ground. The strength is measured in either MPa /
(N/mm2) (ASTM and BS) or psi (ASTM). The compressive strength
is determined in different ways. For ASTM the strength is determined in
accordance with ASTM 109 and for BS and other European countries the
strength is determined in accordance with EN 196-1. Five types
of Portland cement are standardized in the U.S. (Standard Specification
for Portland Cement C 150 - 97): ordinary (Type I), modified (Type II),
high-early-strength (Type III), low-heat (Type IV), and sulfate-resisting
(Type V). In other countries Type II is omitted, and Type III is called
rapid-hardening. Type V is known in some European countries as Ferrari
cement. Five types of Portland cement are also standardized in the U.K.
(Specification for Portland Cement BS 12 : 1996): strength class 32.5N,
32.5R, 42.5N, 42.5R, 52.5N and 62.5N. The different Standard
Specifications for Portland Cement contain different requirements of
chemical and physical properties: MgO, SO3, alkalis as
Na2O, loss in ignition, insoluble residue, Bogue composition,
fineness (Blaine), soundness, autoclave expansion, compressive strength
and initial and final setting. Besides these requirements a standard
specification can contain more specific requirements.
C3S |
- The head clinker component in cement,
typical more than 50 %
- Quick development of strength -
C3S reacts more quickly than C2S
- High contribution to the final
strength
- Resistant to sulphur attack
- 25 weight % water bind under hydration
of C3S
- Heat development: 500 kJ/kg
- Hydration of C3S
(Ca3SiO5 + (y+z)H2O = zCA(OH)2 +
Ca(3-z)SiO(5-z)yH2O) are to some extent
dependent on the presence of C3A and gypsum. Both
C3A and gypsum stimulate the hydration of
C3S. Also Alkalis have some influence at the
hydration.
- C3S =
4.071*CaO-(7.600*SiO2+6.718*Al2O3+1.430*Fe2O3+2.852*SO3)
according to Bogue's methods
|
C2S |
- Second clinker component in cement,
between 10 - 60 %
- Slow development of strength -
C2S reacts more slow than C3S
- High contribution to the final
strength
- Resistant to sulphur attack
- 20 weight % water bind under hydration
of C2S
- Heat development: 250 kJ/kg
- On hydration, C2S
shows similar behaviour to C3S, but is slower to react.
It does however continue to hydrate late in the setting period,
and may then contribute to the strength of the cement.
- C2S =
2.87*SiO2-0.754*(Ca3SiO5) according
to Bogue's methods
|
C3A |
- Range in the cement between 3 -
10 %
- High contribution to the early
strength
- Low contribution to the final
strength
- Not resistant to sulphur attack
- 40 - 210 weight % water bind under
hydration of C3A
- Fast and high heat development: 900
kJ/kg
- Compared with C3S,
C3A reacts very rapidly with water, giving two hydrated
products: 2C3A + 21H = C4AH13 +
C2AH8 These forms platelets within the
cement, and convert to C3AH6, which forms
very quickly, and is responsible for the initial formation of a
crystalline network. In the presence of free lime in the cement,
the formation of C4AH13 is favoured. This
slows the formation of C3AH6, but even so
the formation of C4AH13 can causing the
cement to set too quickly. To avoid speed setting is gypsum added
the cement and the mineral ettringite is formed on hydration:
C3A + 3CaSO42H2O +
25-26H2O =
Ca6Al2O6(SO4)31-32H2O.
- C3A =
2.65*Al2O3-1.69*Fe2O3 according
to Bogue's methods
|
C4AF |
- Range in the cement between 5 - 10
%
- Small contribution to the development
of strength
- 37 - 70 weight % water bind under
hydration of C4AF
- Moderate to low heat development: 300
kJ/kg
- Hydration of C4AF + 13H
= C4AFH13
- C4AF =
3.04*Fe2O3 according to Bogue's
methods
|
Alkalis (Na2O + K2O) |
- Cements with a low alkali content may
be required for use in the manufacture of concrete in which the
use of aggregate introduces silica. Alkalis may enhance reactions
with amorphous silica. The content of alkalis contributed to the
acceleration of the early strength and lowering of the final
strength. The content of alkalis is dependent on the raw materials
but also the manufacturing process decide the content of alkalis.
Cement manufactured by the wet processing will compared to the dry
processing contain less alkalis.
- Alkalis as Na2O =
Na2O + 0.658 * K2O
|
MgO |
- Cements with a high magnesia content
may after setting hydrates and expand.
|
Free
CaO |
- Cements with a high free lime content
may react with water and result in expansion.
| |
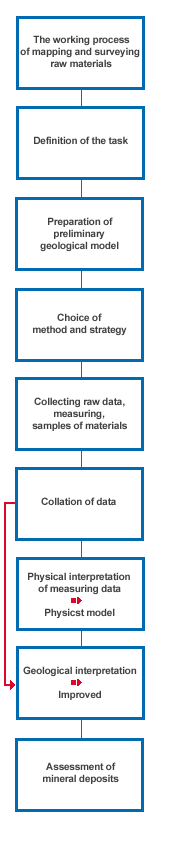 |
Preparing for
the future is very important in the cement manufacturing business. It is
important when founding new cement plants, that the surrounding areas
contain enough raw materials to maintain a cement production for several
years. It is also important to make sure that varying qualities of raw
materials are used consistently and continuously.
The assessment of quality and
quantity of geological materials is a complex process which involves
choice of method and strategy. In the beginning of the working process of
mapping and surveying raw materials, it is important to define clearly the
task and the kind of information the mineral reserve evaluation should
obtain. For most areas geological mapping can be found to various extents.
This information can be used in the preparation of the preliminary
geological model.
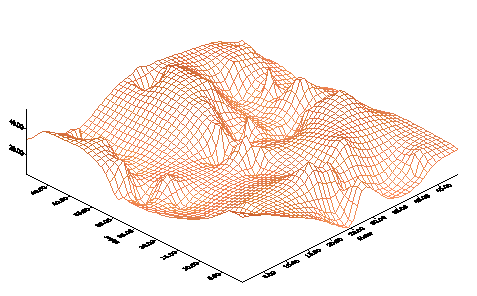
Now method and strategy may be chosen
on basis of task and geological model definitions. The choice of
method depends on what kind of information the mineral reserve evaluation
will obtain. Geophysical methods are used to assess the quantity of
minerals. Today there are several geophysical methods available. The most
common and most frequently used is Direct Current Geoelectrical methods,
but also Alternating Current Geoelectrical methods, Georadar, AMT, VLF,
Seismic and Drillholes Logging can be used. Although these methods are
most useful for the assessment of quantity, they may also be used as a
tool for an overall geological interpretation of the area.
In order to assess the availability
and quality of raw materials for cement manufacturing, the samples must be
obtained as core samples from drillholes and analyzed using XRF. The
results from the XRD analysis are usefull tools in mapmaking. By using the
results from the XRF analysis (drillholes) related to the position
(X-coordinate and Y-coordinate) of the basemap of the area, valuable maps
can be made to optimize the coefficient of utilization of raw materials
and maintain a uniform quality of raw materials intended for the
production. The same procedure is of utmost importance when founding new
cement plants.
The first task is to collect the
input data. The data falls into four categories:
- Drilling data (which includes the
surface elevation of the drillhole, depth at which the horizon of the
materials was encountered, thickness of the formation, a lithology
description, the X-Y coordinates and core samples).
- Laboratory analysis data
(qualities of samples from drillholes, based on XRF analysis).
- Surface topography data (which
includes thickness of overburden).
- Property and planning maps (which
include mining property boundary, barriers to operations such as
highways, railways and property ownership).
The process of manufacturing contour
maps based on X-Y-Z data set involves:
- Data checking and
validation
- Selection of gridding
method
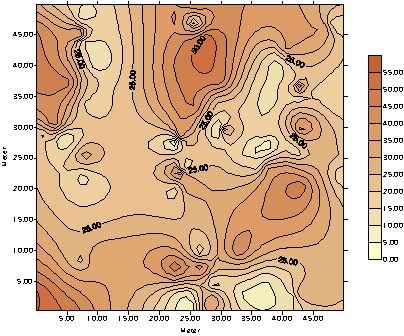
|
Sr.# |
Name of Machine |
Description |
Manufacturer |
Mfg. Year |
1 |
Kiln (Vertical shaft) #2 |
50 TPD |
|
- |
2 |
Reciprocating Feeder |
- |
|
- |
3 |
Hammer Mill |
- |
|
- |
4 |
Roller Mill #2 |
- |
|
- |
5 |
Ball Mill |
- |
|
- |
6 |
Jaw Crusher |
- |
|
- |
7 |
Conveyor (Screw) |
- |
|
- |
8 |
Conveyor (Belt) #5 |
- |
|
- |
9 |
Conveyor (Bucket) |
- |
|
- |
10 |
Rotary Feeder #4 |
- |
|
- |
11 |
Raw Mill #2 |
- |
|
- |
12 |
Cement Mill |
- |
|
- |
13 |
Nodulizer #2 |
- |
- |
- |
14 |
Table Feeder #2 |
- |
- |
- |
15 |
Crusher |
- |
- |
- |
16 |
Blower |
- |
- |
- |
17 |
Bucket Elevators #7 |
- |
- |
- |
18 |
Silo (Blending) |
- |
- |
- |
19 |
Silo (Storage) |
- |
- |
- |
20 |
Packing Plant |
- |
- |
- |
21 |
Feed hopper |
- |
- |
- |
22 |
Transformer |
1500 KVA |
- |
- |
23 |
D G Set |
15 KVA |
- |
- |
24 |
Motors #lot |
- |
- |
- |
25 |
Quarry Equipments #lot |
- |
- |
- |
26 |
Workshop Equipments #lot |
- |
- |
- |
27 |
Laboratory Equipments #lot |
- |
- |
- |
28 |
Misc. Electrical Tools #lot |
- |
Cement Kiln Flue Gas recovery Scubber
http://www.lanl.gov/projects/cctc/factsheets/pass/cemkilndemo.html
Perhaps the most important thing to understand about concrete is the role of water. First, it provides plasticity so the concrete can be poured in a form. Its real importance, however, is in the hardening process. Wet concrete doesn’t harden by drying. Instead, the water is a chemical component in a curing process. The compounds that react with the water are in the portland cement.
Isle Of Portland While cement in one form or another has been around for centuries, the type we use was invented in 1824 in Britain. It was named portland cement because it looked like the stone quarried on the Isle of Portland.
Portland cement is produced by mixing ground limestone, clay or shale, sand and iron ore. This mixture is heated in a rotary kiln to temperatures as high as 1600 degrees Celsius. The heating process causes the materials to break down and recombine into new compounds that can react with water in a crystallization process called hydration.
Concrete cures in several stages—a factor that allows it to be trucked to the job site and still be ready to pour. With the concrete in the form, the cement begins a slow cure and the mix hardens. After about 36 hours, most of the hydration process is complete, but the cement will continue to cure as long as water and unhydrated compounds are present. While the process can take years, strength tests are typically done after 28 days. It’s important to use the right amount of water. Too much makes for weaker concrete. However, too little makes the mix hard to pour. The best mix is a compromise between strength and workability.
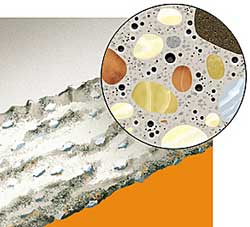 |
|
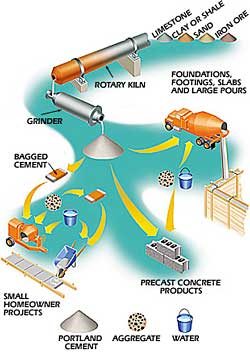 |
Concrete is a combination of hydrated portland cement and aggregate. Common aggregates are sand and gravel. Air-entrained concrete has tiny bubbles to help prevent cracking. |
|
Concrete starts with the production of portland cement in the rotary kiln and grinder. From there, it’s packaged in bags for on-site use, mixed for truck delivery or used to produce concrete products such as blocks and pavers. |
From Cement To Concrete While cement and water are the active components, it’s not economical to use them alone. Instead, aggregates are added to increase the volume and tailor the concrete to its final use. Typically, 60 to 80 percent of the concrete is aggregate. In most cases, the aggregates are sand and gravel. When sand is used alone, the result is mortar. When both are present, the result is concrete. However other aggregates might be used depending on the required characteristics of the cured mix. For example, vermiculite or perlite aggregates produce a lightweight concrete that has good insulating properties and can be easily sawn.
Improving Performance Concrete suppliers often use additives, called admixtures, to alter or improve the qualities of the mix for a specific application. When it’s important to have a workable concrete that pours easily without adding extra water, a mineral additive such as fly ash is added. Alternatively, superplasticizers are used to improve workability while increasing strength because less water is required. Retarding and accelerating admixtures are used to alter curing time as necessitated by climatic conditions.
One problem with concrete is a tendency for freeze/thaw cycles to cause cracks. To help remedy this, air-entraining agents are added. These admixtures create a dispersion of very fine air bubbles that cushion the concrete against the effects of freezing water.
Buying Concrete The form in which you buy concrete depends on the size and nature of your job. Concrete is normally measured in cubic yards. To determine how much you’ll need, figure the volume inside your forms in cubic feet and divide by 27 (the number of cubic feet in a cubic yard). For example, a 4-in.-thick slab that covers 90 sq. ft. takes up 30 cu. ft., or just over 1 cubic yard. Projects using up to about a cubic yard can be handled with a portable cement mixer that you can rent. The proportions of cement, sand, gravel and water can vary depending on the use of the concrete. For example, thin work—between 2 in. and 4 in. thick—will require more cement, whereas a higher-mass pour can afford to use more aggregate. An average 1:2:3 mix contains one part cement, two parts sand and three parts gravel. To make 1 cubic yard of concrete, you’d need seven 94-pound bags of cement, about 1/2 cubic yard of sand and just over 3/4 cubic yard of gravel. The amount of water you use depends on how wet the sand is. If it’s already moist, you’ll need about 4-1/2 gal. per bag of cement.
For smaller projects, you can buy premixed bags that contain cement and aggregate—you just add water. For bigger jobs, the best route to take is ready-mix concrete. In addition to the obvious advantage of having the concrete delivered, your supplier can also tailor the mix and admixtures for your job. Ready-mix prices vary based on the distance of the delivery, the type of mix and the size of the order, so it’s best to call a local dealer for a price. If your site is inaccessible to the truck, you may be able to have the concrete pumped through a hose. Or, you can simply carry the concrete from the truck with wheelbarrows.
Finally, you may be able to avoid the pouring entirely by using finished concrete products. Concrete block is available in a variety of sizes, structural qualities and surface styles for building walls that might otherwise be poured. Traditional block walls are built with mortar, but blocks designed to be laid up dry are also available. In addition, concrete pavers, bricks and small slabs are available for landscaping and walkway projects.
|
 |
|
 |